ERPNext Case Study: Transforming Garment Manufacturing and Distribution
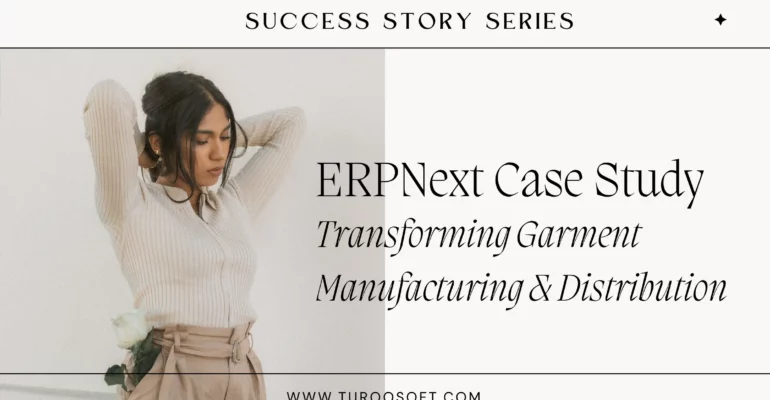
ERPNext Case Study: Transforming Garment Manufacturing and Distribution
In this ERPNext case study, we dive into the transformative impact of implementing a customized solution for a prominent Garment Manufacturer and Distributor. We’ll unravel the challenges faced by the client, detail the extensive ERPNext deployment process, and highlight the key features that played a pivotal role in overcoming obstacles.
ERPNext Case Study
Collaborating closely with this prominent industry player, we navigate through the intricacies of the ERPNext implementation, shedding light on how this tailored solution brought about remarkable outcomes, fostering efficiency and growth in the competitive landscape of garment manufacturing and distribution.
Client Profile:
The client, a prominent player in Garment Manufacturing & Distribution, faced operational challenges. The absence of a centralized system hindered real-time insights, impacting decision-making and growth potential.
Challenges:
- Inefficient Operations
- Lack of Real-time Insights
- Disparate Systems
Our client, a key player in the garment manufacturing and distribution sector, struggled with productivity and decision-making due to inefficiencies spanning Inventory Management, Sales and Distribution, Purchase, Manufacturing, Accounting, HR, and Payroll. The absence of a centralized system hindered real-time insights, impacting their growth potential.
Solution:
The solution involved a meticulous analysis of unique challenges, leading to a customized ERPNext deployment. Seamlessly managing Inventory, Sales, Distribution, Purchase, Manufacturing, Accounting, HR, and Payroll, it addressed the client’s diverse business processes effectively.
Objectives:
- Streamline and centralize diverse business processes.
- Enhance real-time visibility into operations.
- Facilitate seamless coordination across departments.
- Improve decision-making capabilities.
- Increase overall operational efficiency.
Deployment Process:
Our expert team meticulously analyzed the client’s unique challenges and meticulously crafted a customized ERPNext solution. The deployed system seamlessly managed critical operations such as Inventory, Sales and Distribution, Purchase, Manufacturing, Accounting, HR, and Payroll.
Key Features:
Key features of the ERPNext implementation included acting as a centralized hub, fostering seamless coordination across departments, providing real-time insights for informed decision-making, enhancing overall decision-making capabilities, and automating processes for streamlined efficiency.
Centralized Hub
The ERPNext solution acted as a centralized hub, integrating various systems into a seamless platform. This holistic view of operations led to enhanced coordination and improved decision-making capabilities.
Seamless Coordination
By breaking down silos and fostering collaboration, the integrated platform facilitated seamless coordination across departments. ERPNext improved communication, workflow efficiency, and minimized response times by eliminating manual handoffs and enhancing real-time data synchronization.
Real-time Insights
Real-time data synchronization provided valuable operational insights, empowering the organization with informed decision-making capabilities. ERPNext offered up-to-date information on inventory levels, sales trends, production timelines, and more. This real-time visibility allowed proactive bottleneck identification, process optimization, and adaptation to evolving market demands.
Enhanced Decision-Making
With a holistic view of business processes, ERPNext significantly improved decision-making capabilities. Comprehensive analytics and reports enabled data-driven decisions, identification and pursuit of growth opportunities, and effective risk mitigation.
Streamlined Processes
Automation and streamlining reduced manual intervention and minimized errors. ERPNext automated routine tasks, including order processing, inventory tracking, and payroll management. These improvements optimized resource allocation, allowing the workforce to focus on value-added activities.
Outcomes:
The successful ERPNext implementation resulted in transformative outcomes, including a significant boost in operational efficiency, proactive decision-making empowered by real-time visibility, cost savings through streamlined processes, improved customer service, and scalable solutions for the client’s expanding business.
Operational Efficiency
Streamlined processes significantly boosted overall operational efficiency, reducing lead times, increasing productivity, and enhancing resource utilization. Our client effectively met customer demands, minimized production bottlenecks, and optimized inventory levels.
Real-time Visibility
Proactive decision-making was empowered by real-time visibility into operations. ERPNext provided accurate and up-to-date information, facilitating monitoring of performance, identification of emerging trends, and swift informed decisions. This real-time visibility enabled prompt responses to market changes, customer demands, and production challenges.
Cost Savings
Automation and process optimization resulted in significant cost savings. Manual data entry was eliminated, reducing errors, enhancing inventory management, and leading to improved forecasting capabilities. These improvements minimized stockouts, overstocks, and wastage, ultimately enhancing profitability.
Improved Customer Service
Enhanced coordination allowed timely and effective responses to customer needs. By leveraging ERPNext, our client improved order processing, ensured on-time deliveries, and provided accurate information to customers. Consequently, customer satisfaction, relationships, and customer retention rates improved.
Scalability
The scalable nature of ERPNext ensured alignment with our client’s expanding business. As their business grew, ERPNext accommodated changing needs, facilitating seamless expansion. The solution’s flexibility allowed for managing a larger customer base, increased production capacity, and swift adaptation to market fluctuations.
Conclusion
The successful deployment of our custom ERPNext solution has revolutionized our client’s operational landscape, positioning them for sustained growth and success in the competitive garment manufacturing and distribution industry. This case study is a testament to our commitment to delivering tailored solutions that empower businesses to thrive in the ever-evolving business landscape.
By implementing ERPNext, our client experienced improved efficiency, streamlined processes, enhanced decision-making, cost savings, and improved customer service. Contact us today to transform your business with ERPNext!
If you’re seeking expert guidance for the seamless implementation and customization of ERPNext, unlocking its full potential for your organization, look no further. Reach out to us, and our seasoned team will be thrilled to provide the assistance you need.
Feel free to drop us a message, either via email at info@15.206.92.4 or by giving us a call at +91 9841205845.
Alternatively, stay connected with us on various social media platforms such as LinkedIn, YouTube, Facebook, Twitter, Pinterest, or Instagram to receive regular updates on ERPNext and other pertinent topics.
Image Credit: Canva
Comment (1)
Sebastian
I really enjoyed the standard information a person supply to your visitors